How to Compare Teak and Composite Decking
Teakdecking Systems (TDS) offers legally sourced superyacht-quality Southeast Asian teak and high-end polyurethane composite decking. Boat owners often ask us how to compare teak and composite decking. Rarely is there one factor alone to consider. All these must be weighed: appearance, durability, maintenance, safety, cost, installation, deck weight, environmental impact, and surface temperature. Here, we look at each factor to compare teak and composite decking.
APPEARANCE
TEAK is traditional, classic, and timeless. It has a “warm” feeling, especially when it is new or after sanding. Sunlight ages it to a silvery patina. Superyacht quality teak has tight grain quarter-sawn teak from old-growth Burmese logs and is highly durable. So, many consider it a status symbol. Some enthusiasts even consider it “obligatory” for wooden boats.
COMPOSITE decking provides freedom of design to create unique decking—contemporary or traditional. The color and texture can be customized, and the color stays true for an extended time. Unlike teak, butt joints are not necessary. Like teak, it does not absorb water.
DURABILITY
TEAK is exceptionally durable and can last 15-20 years or longer with proper care. See our blog on “How to Extend the Life of a Teak Deck”. Its wear is dependent upon usage and desired look (or sanding frequency). Teak is rot-resistant; its natural oils fight water penetration, as well as algae and mold. Red wine or fish blood can and will stain teak, but can easily be removed. Sunscreen and potato chip oil will penetrate the wood (and can stain too). TDS Sealer and Protector can safeguard the surface. Soiled or damaged teak battens or trim boards can be sanded, repaired, or replaced.
COMPOSITE decks can last 20 years or more. This is achieved with well-installed, properly maintained, high-quality materials, such as the polyurethane of TDS Composite Decking. These materials resist shrinkage and adhesive failure when installed properly. In contrast, lower quality composite decks (EVA and PVC materials) can last as few as three to five years.
Properties vary by material type. In general, composite materials are stainproof from many fluids, but not red wine and fish blood. Quite often, the decking discolors (fades) over time even though some materials have UV inhibitors to reduce the effects. Some inferior composite materials will shrink, and adhesive failures can occur. Repairs and refits typically require trained professionals.
MAINTENANCE
TEAK is gently cleaned by scrubbing across the grain with a medium scrubbing pad (3M “red”) and a one-part cleaner (ECO-100 & ECO-300). For more aggressive restoration, a sand-out may be needed. NOTE: Power washing or vigorous chemical cleaning (two-part cleaners) removes softwood, leaving hard ridges that hold dirt and contaminants. Harsh cleaning methods can also harm the surrounding gel coat or paint and stainless steel.
COMPOSITE is easy to clean with water, soap, or by power washing. Skin oils or scuffs show immediately on some light-colored materials but are cleanable.

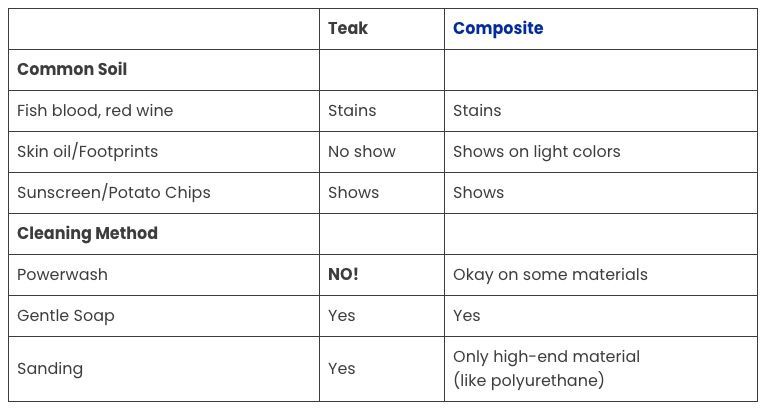
SAFETY
TEAK is a natural, non-skid surface, wet or dry, and COMPOSITE materials have the same properties.
“Endeavor” Photo credit: Kos Holland
COST
TEAK supply of legally sourced old-growth trees is diminishing; timber costs are steadily increasing. So it is tempting to consider lower-priced plantation teak as an alternative. This is not recommended since it is less durable (more softwood) and the much wider grain gives in an aesthetically unsuitable appearance. If well-maintained, teak will significantly enhance a vessel’s resale value.
COMPOSITE materials are 30-50% less expensive than teak, according to many industry publications. However, quality can vary widely depending on the manufacturer. Installation costs vary too. High-end materials with professional installations can be priced slightly less than teak.
INSTALLATION
TEAK decks can be installed by a moderately skilled carpenter for most projects. TDS or a qualified boatyard should install more complex projects (e.g., lots of trim and hatches). This is especially true when performing fastenless installations, i.e., vacuum bagging and barring. Some small areas can be DIY. Repairs to teak can require the replacement of batten(s) or margin trim.
COMPOSITE is best installed by a moderately skilled carpenter. The fairing of the subdeck must be virtually perfect for the thin panels (e.g., 6mm). Improper installation can cause “bubbling” by adhesive gassing or trapped air. This problem occurs when cure times are not met, or when the “down” pressure is removed too soon.
Note for DIY: Achieve the best results by having the manufacturer pre-cut the decking panels to address the many styling details. Understandably, the best areas for DIY are small, like an interior sole or footrest. Some materials are “peel and stick.” As previously mentioned, a replacement may be needed in 3 to 5 years from installation.
DECK WEIGHT
TEAK weight varies with the thickness; the most common thickness is 14mm with an estimated weight of 2.2 lbs/sq. ft (10.7 kg/sq m). For a slight weight reduction, the teak thickness can be reduced to 10mm or 12mm.
COMPOSITE weights vary by product type (EVA, PVC, etc.); however, most are lighter than teak.
ENVIRONMENTAL IMPACT
TEAK must be legally-sourced from sustainable forests. (Note: TDS timber is 50+ years old.) The use of elephants for harvesting and transporting logs helps protect endangered species. It also aids new growth teak, with less impact on the land. 90% of a cut teak tree is used in multiple industries for decking, furniture, windows, doors, etc. Teak is renewable and recyclable.
COMPOSITE decking may have oils and chorine used in its production, and hazardous by-products are produced. Some materials are not recyclable and not as “green” as desired. It is best to check with the product manufacturer for more information.
TEMPERATURE
TEAK has the coolest surface, in general. The R-value (insulation) and sound suppression are very good. Further, below deck temperatures are more stable due to teak’s insulation properties.
COMPOSITE PVC decks can get as hot as 150°F (65.5°C). Lighter-colored materials have the coolest temperatures, and darker colors can become too hot for bare feet. (TDS firmly recommends light colors.) The lowest density material will have the lowest heat. Composite decking will cool when wet.
SUMMARY
Owners have the freedom to decide on decking, and these are 3 KEY TIPS to compare teak and composite decking:
- Consider the boat type and the amount of maintenance required.
- Research all materials and select one based on performance and personal taste.
- Purchase within budget.
Read more about composite decking in this article: “Wood” You Know the Difference?
To discuss your project with an experienced project manager, please contact us:
941-756-0600, press “1”
yacht.services@teakdecking.com
ALL PRODUCTS
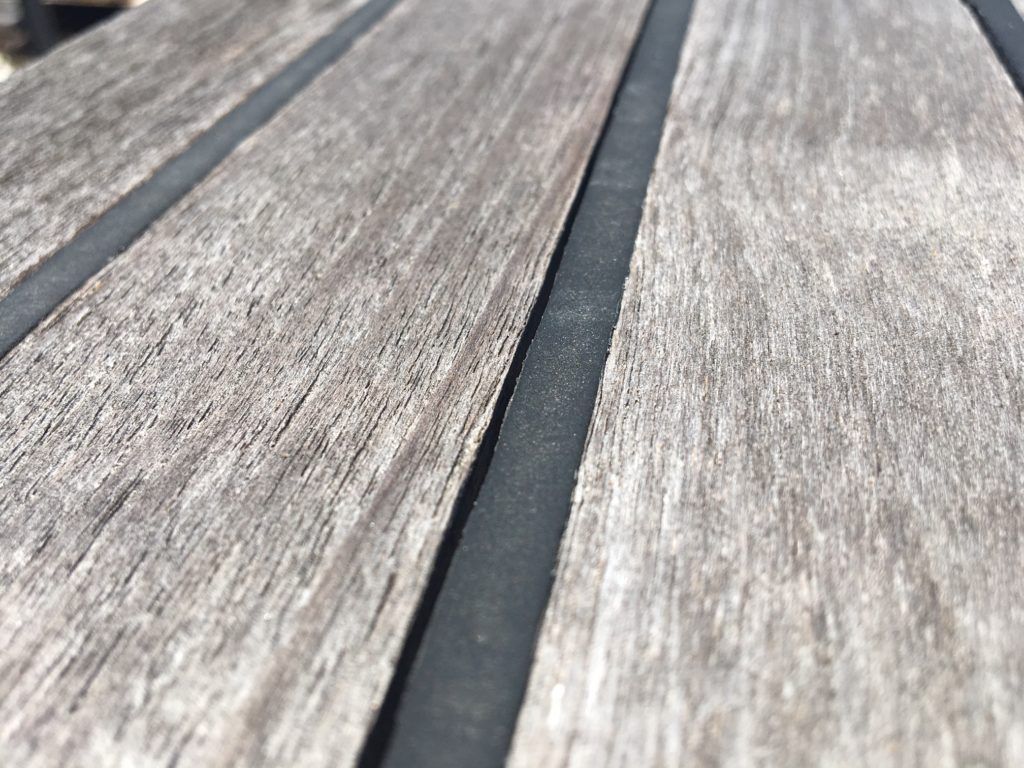